Whether you are in the market for a mixer (sometimes called a blender) to integrate into an existing processing line or you are looking for equipment to support a start-up, selecting quality equipment is critical. Mixers (or blenders) can operate for decades when properly maintained, and whatever equipment you select today will be a part of your operations for the foreseeable future. While less expensive machinery may be appealing from a cost-savings perspective, it can carry its own hidden expenses and lasting negative implications. Rethinking a mixer as an investment with longevity rather than as a short-term processing solution will ultimately serve to benefit your business in the long run.
There are some hallmarks of a quality machine you will want to keep an eye out for, and a few features to take into consideration:
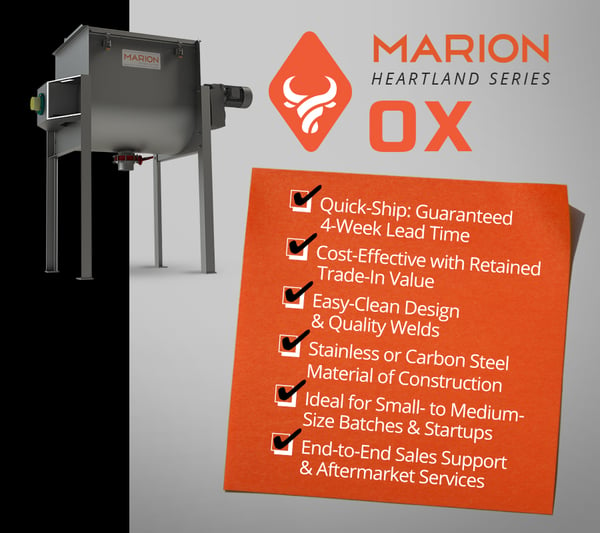
Manufacturing Quality: Real Steel
Industrial mixers are designed to handle a wide variety of materials. Look for equipment fabricated with quality steel that will withstand wear and tear over decades of use. Additionally, verify that your prospective equipment manufacturer can provide supporting documentation that shows where they source their steel from as well as its material composition – especially if you require stainless steel.
Solid Shaft: Quality Now, or Downtime Later
One common cost-saving measure in mixer construction is the use of a hollow shaft on the agitator. While this may save on upfront costs, they lack the inherent strength and durability of a solid shaft. A shaft failure is not an easy fix, resulting in labor, material and downtime costs that can quickly add up. Look for a solid steel shaft to ensure reliable performance and increased lifespan.
Welding: Keeping It All Together
Quality welds are critical to the long-term performance of a horizontal batch mixer. MIG (Metal Inert Gas) welds utilize a continuous wire feed to form welds, and offers a more efficient weld with shorter fabrication times. Ask your manufacturer about how they weld, as well as how they test those welds to ensure quality.
Motors and Bearings: What’s in a Name?
Whatever manufacturer you choose, they should be an expert in mixing technology, that’s a given. You should, however, expect them to partner with name-brand, expert suppliers for non-mixing parts like motors and bearings, and stand behind the equipment they integrate into your mixer.
Parts: The Cost of Replacement
Regular maintenance is key to keeping cost of ownership low over the life of your mixer. Part of that process is the regular replacement of soft parts: gaskets, valves, and the like. Does your supplier offer aftermarket support? Can they offer the parts with short turn-around times to avoid downtime? And is their suggested maintenance schedule realistic, manageable, and tailored to your process?
Installation, Consulting and Aftermarket
Whatever mixer or blender you choose, you need to make sure that the relationship extends past the sale. After all, you’re not just buying a piece of equipment, you’re investing in your company’s future. Your manufacturer of choice should offer installation and start-up assistance, a network of skilled suppliers, aftermarket support, and testing, either on-site or in a lab. Essentially, this should be the beginning of a long-term relationship – not just order fulfilment.
Summary
Choosing the right mixer/blender needs to be a balance of acquisition cost and cost of ownership. Make sure you consider the following before you decide:
- Steel that you can source and know the quality of
- A solid shaft to avoid costly replacement
- Quality welds that undergo QA testing
- Reliable, outsourced parts from known suppliers
- A preventive maintenance plan and readily available aftermarket parts
- A network of suppliers and support to help after the sale
Visit the new Heartland Series for more information.
Configure your Ox Today!