Each day hundreds of millions of people all over the world consume food products that have been through some sort of processing plant. From meat and vegetables to drinks and desserts, each one must pass the highest regulatory standards to ensure consumer safety. As the population continues to grow at a rapid pace, so does the need for processing of food items across the world. Add to the mix the rise of the big box stores and the demand for convenience products and it’s no wonder that the food processing industry is challenged with finding the safest most efficient solutions to get products to the market in a timely fashion.
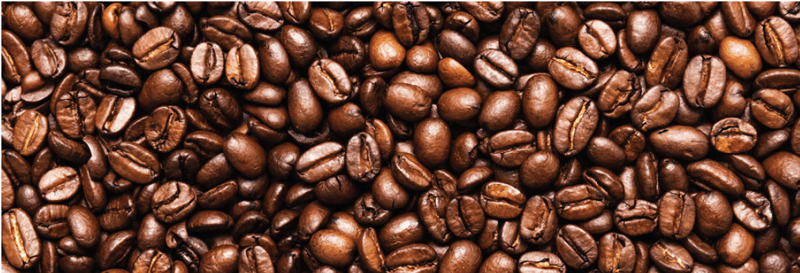
Every year food-borne illnesses cause roughly one-in-six Americans to get sick with 128,000 hospitalizations, and 3,000 deaths. Because of this, it’s important that food processing plants keep up with changing mandates and standards. One of the most important is the Food Safety Modernization Act (FSMA), which became law in 2011. When choosing the right mixer (sometimes called blender) for food processing, it’s critical to work with a company that is 3-A authorized to ensure the best in safety and sanitation.
We’ve got the Numbers to Prove it
Marion Process Solutions is the only 3-A authorized manufacturer of horizontal mixing equipment - elevating safety and sanitation to an entirely new level. We have over 80 years of experience in working with thousands of applications, so we’ve learned a thing or two along the way. When we say, there’s safety in numbers, we’ve got the numbers to prove it.
Here are some factors to consider when choosing the right mixing solution for your specific food application:
- Product Type: Choosing between paddle or ribbon agitators and determining the trough shape depend on the product attributes
- Batch Size: Properly sizing your mixer (or blender) is essential to creating a successful mix
- Mix Time: Batch or continuous, our mixers and blenders are designed with the optimal mixing time in mind
- Product Input: Always mindful of safety, we start with a blank canvas and design our covers based on how product will be metered into the mixer or blender
- Product Output: Considering the properties of the product being mixed and the overall layout of the mixer/blender affects the type and location of the discharge mechanism
- Sanitation: The 3-A symbol is more than a logo, it’s a commitment to upholding the highest standards in the design, materials, and fabrication of our equipment
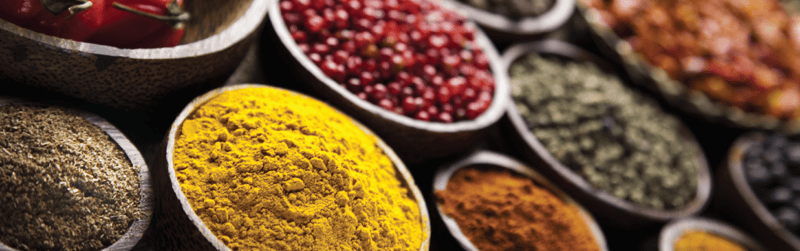
Bringing more to the table
With custom-designed solutions built to solve specific needs, Marion mixers/blenders elevate the entire industry. The following innovations and features set Marion apart from the competition and have made Marion the provider of choice for companies such as General Mills, Kraft, Kellogg, Nestle and Quaker.
- O-Ring Design: Marion’s innovative design provides a far superior seal compared to competitive products. The seal is completely sanitary, as well as easily removable and replaceable for cleaning.
- Double Lip Seal: Designed in response to seal failure issues with third party products, Marion created a seal that is easier to clean and install, meets 3-A, FDA and USDA guidelines, and has a much longer lifecycle.
- Removable Spray Bar Manifolds: Creating a removable version allows for quicker changeover and cleaning between batches.
- Wavemix™: Industrial microwave, vacuum and mixing technology is ideal for processing low-moisture, low-temperature, or applications requiring microbial reduction.
When it comes to keeping your facility safe and sanitary, it’s best to go by the numbers. Marion Process Solutions is the only manufacturer who makes the grade as the ONLY 3-A authorized provider of blending equipment in the United States. Trust us with your next batch and contact one of our experts for more information on how we can customize a solution for you. Subscribe to our blog to continue to get updates from us.