When making a purchase of a mixer or blender for any type of industrial processing, there is only so much you can read and learn. In the end, you want to know how the machine will perform. Any reliable vendor will have several machines at their facility where you can test the equipment on your actual formulation. Whether it’s food, chemical, biomass, nutraceutical or pharma—you need to know the equipment works. In some ways, testing is one of our favorite ways that we can help our customers.
By the way, that’s the first sign you are working with the original manufacturer, not just a channel partner or white-label. If the mixer or blender vendor is sending samples somewhere in a far away land, you have to wonder how the installation and site testing will go. In other words, the testing of your materials is also a test of whether you are working with a vendor you’ll be able to count on in the long run for parts, service and problem solving.
Marion’s testing lab team is experienced with hundreds of types of food mixes as well as biomass, chemicals, plastics and pharmaceuticals. Working with an experienced test lab team provides industry benchmarking. Working with a company with more than 80 years of experience is a completely different experience from working on your own, so it makes sense to avail yourself of the testing services offered.
Basic Testing
At Marion, initial testing is typically free of charge. We welcome site visits when possible. Recently, we’ve installed a video setup so that if travel is impossible, you can still get the feel of being right there with us in the laboratory. That is particularly important because nobody knows your mix better than you. We have an amazing team of technicians and engineers with decades of experience, but it’s always best to have our customers working closely through the test.
Usually our basic test includes three runs of the material. The first test is our best guess on the setup, based on similar mixes. We look at those initial results together, make the appropriate adjustments and then run a second test. The third test allows us to tweak some parameters and have comparisons.
Mixers, sometimes used synonymously with blenders, vary in the types of paddle, shape of trough, loading procedures, speed and time of mixing, timing of adding ingredients, etc. If you are with us in person or through video during the process, we discuss these adjustments together for the best results. Whether or not you take part in the process, you’ll get a comprehensive report showing all of the tests and parameters, as well as your materials post-processing, shipped back to you for your inspection.
The Testing Process
We like to say that testing is a 7-step process. There is a lot more going on behind the scenes, of course, but let’s take a look at the process itself:
- Collecting customer needs: You’ll fill out a one-page test form which tells us what we’ll be testing, your expectations and the results that you consider ideal.
- Safety overview. We fill in a Safety Data Sheet to make sure our labs will be prepared for whatever you’re sending over. As most manufacturers know, something as run-of-the-mill as flour dust can be combustible. We comply with all regulatory requirements and maintain a high level of safety standards.
- Waste determination. Generally, our policy is to ship back all materials post-testing, but some manufacturers just want a sample and prefer for us to dispose of any leftover material. We’ll go thorough any special requirements and potential disposal costs if relevant.
- Test scheduling. Together, we’ll schedule the right time for the test, set you up to ship the materials to us, and get ready for testing day.
- Test planning. Planning and preparing is our job. We’ll confirm delivery of the materials and store them properly, get the right machines set up in the laboratory and prepare ourselves for your visit. We also prepare for packaging the samples for shipping back to you. Some customers have special requirements for how they want the samples to return.
- Test day. We encourage our customers to come visit our world-class testing facility. If it’s logistically feasible, we would love to have you in for a full day that includes a tour of the facility, safety briefings, testing, a debrief, and of course, lunch together. Marion Process Solutions is about a half hour drive from the Cedar Rapids airport, so you can get to us easily. If you can’t make it to the facility, we’ve set up live video streaming capabilities so you can be with us virtually during the tests.
- Test summary. You’ll receive reports with the testing parameters, testing results and photographs of the materials. We will also ship your mixes back to you, so you can see and feel the results for yourself. The reports aren’t just for reporting purposes, of course. They’ll serve us later for factory acceptance tests and site tests, so you’ll always be able to configure the machines for consistent, reliable results.
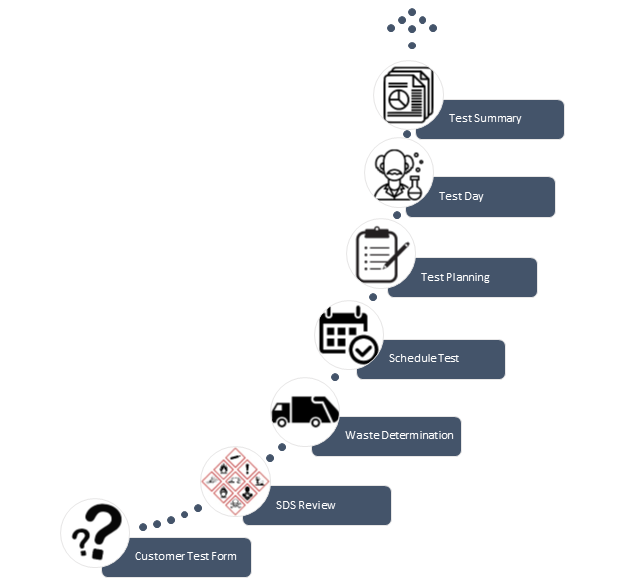
Deeper Testing and Tweaking
Test labs are not just for trying out equipment; we can also do more extensive testing to perfect a mix, try different thermal processing configurations, or experiment with new materials. While these deeper tests are not free, they pay off in the long run. When creating new formulations, optimizing for quality or improving existing processes, testing multiple variables in the laboratory allows our existing customers to save time and improve their existing product lines without taking any of their machines offline.
Every Marion machine is customized. For precision results, sometimes clients will want to run extensive testing and tweak different configurations before confirming the final tooling of the machine. Perfection in every machine leads to lower operating costs, better quality and long-term fit of the machine for your specific needs.
In Summary
OK, we will admit it. The reason we want you to test is that once manufacturers see the quality and efficiency of our mixers, they never go back to their old vendors. We made the investment in our test laboratory so we can show off. Yes, we are proud of our made-in-the-USA mixers and we’re proud that our mixers produce visibly superior results. But do not take our word for it. Sign up for a test today and find out for yourself.