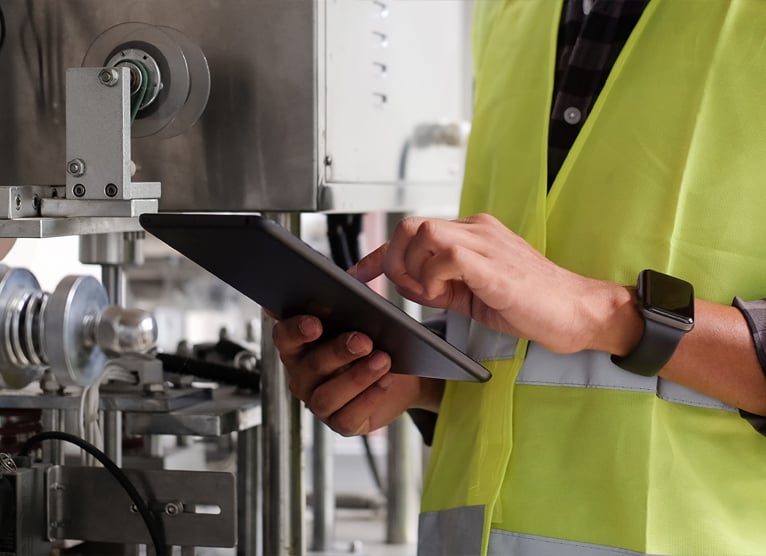
Successful material processing equipment installations don’t happen by osmosis.
It takes careful planning and a keen understanding of how your equipment works to avoid the kinds of hiccups that can lead to installation delays, unplanned construction costs and ultimately lost production time.
Over the years, Marion’s field service technicians have been involved in hundreds of installations on equipment ranging from horizontal mixers and lump breakers to V-cone and double cone blenders. Some we’ve overseen directly and others required our team to be brought in after the fact to address a costly mistake.
Fortunately, many of these mistakes can easily be avoided if you know what to look out for ahead of time. To ensure your next equipment install goes smoothly, here are three of the most common mistakes we’ve seen (and what you can do to address them).
- The space isn’t prepped to receive equipment
Have you taken the proper measurements to ensure your facility has the right amount of clearance so your equipment can easily be moved into place? Is the floor that your equipment will sit on level?
We’ve been on job sites where walls have had to be torn down, floors have had to be shimmed and electrical work needed to be extended to reach the machine. Making sure these things are done correctly ahead of time means you won’t have to scramble to purchase materials, hire contractors to perform additional work and push back your launch date.
- The contractor (or member of your staff) doesn’t understand the equipment
It may sound like common sense, but having work done by people who don’t fully understand how your equipment works can really cost you. In one case, we were called into a facility where the mixer was running backwards after an electrician installed new controls incorrectly.
Many times we’ve been called to fix burned out chopper motors that could have been easily prevented had someone followed the equipment’s maximum allowed run times. Even more frequently, we’ve seen screens that were installed up-side-down, which had a direct impact on performance and product quality.
To avoid these kinds of issues, it’s a good idea to have the equipment manufacturer on-site to provide startup assistance. That way, they can chime in and provide assurance that your contractor or staff is following the right procedures.
- Not taking upstream and downstream flow rates into account
Calculating the speed that your material is being conveyed into and out of your machine so that it falls in line with your machine’s flow rate tolerances is another area where mistakes can happen.
You might measure the average flow rate, but forget to factor in how high the flow rate can spike from time to time. Not taking these extremes into account means you run the risk of burning up the motor and damaging your machine fairly quickly.
The good news is that many of these common mistakes can be averted simply by having a knowledgeable technician on-site to supervise the installation and start-up process. While it can be tempting for customers to take on these responsibilities by themselves, it is not always in their best interest to do so.

Want more education on servicing your processing equipment?
Check out these resources:
“3 Mixer and Blender Parts to Keep on Hand to Avoid Downtime”
“The 6 Things to Check Before Ordering Processing Equipment Parts”
“When Refurbishing Makes More Sense than Buying New”