Thermal Processing Equipment Benefits for Cannabis
Cannabis as a whole represents an exciting business opportunity, especially given the explosion of the global hemp market, which is projected to grow at a compounded annual growth rate of close to 35% per annum over the next 5 years.
Business people are racing to take advantage of the cannabis opportunity, but like any business opportunity, cannabis processing has its unique characteristics and challenges. Many people are jumping into the industry without realizing the complexities involved. In the best case, they get some advice beforehand, but in most cases, after jumping in, they come up against a variety of issues, and begin to desperately seek solutions. If you do a search, you’ll find there’s plenty of advice out there, from cultivation to processing to retailing, but where is it all coming from?
Unfortunately, a tremendous amount of “expert” advice is coming from experts who have no more experience than the people seeking their expertise. In such a new industry, there is no way to prove the results of any of these experts over time. So, let’s be honest. As a company in the heart of Iowa, our expertise is specific. We aren’t growers: we are specialists in the processing of the products that farmers produce. For more than 80 years we have been working with biomass products. Hemp is just the newest one on the market, but as you can imagine, in our 80 years, we’ve seen new variations of biomass products, well, just about every time a new season comes around.
When it comes to hemp and cannabis, drying is a hot topic. So let’s talk about cannabis and drying technology from the perspective of the real experts: people who have been working with thermal processing for biomass, consumables and pharmaceuticals for decades, and with cannabis since it’s become a serious opportunity.
Thermal Processing: Let’s Talk Terminology
If you come from other industries, you may not be as familiar with the term “Thermal Processing,” which simply means changing or regulating the temperature of materials during processing. A variety of thermal processing is used in foods, pharmaceuticals and biomass products to speed production, manage product quality, and produce unique products.
As with other industries, cannabis processing requires precise results from the drying process. The value of cannabis can be directly impacted by the drying output. Ideally, the moisture content of dried material is in the range of 10–20%.
Choosing the right drying method makes the difference for your production line, and this article gives information on both traditional air drying and bulk industrial methods of cannabis drying. If you are looking into the potential of using industrial methods for large batches of cannabis, this article will help you make the right decisions.
Air Drying
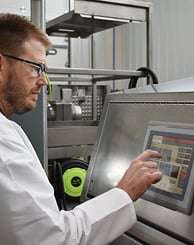
For small production rates of cannabis, hanging the plants to dry is a time-tested technique. To effectively use this methodology, processors need to create an ideal drying environment with ambient temperatures between 60-70° F and humidity of 60%. Whole plants or flowers are suspended, leaving enough space to allow for high air flow. Depending on the starting moisture content of the material, drying is typically achieved in 72-240 hours.
Unfortunately, gravity is working against processors using this method: a hanging plant tends to collapse on itself, restricting the movement of air to the inner areas, putting the plant in danger of developing mold and mildew growth. One way to combat mold is to break off and hang individual branches; however, this is a time-and labor-consuming process. A typical acre of cultivated hemp contains 1,000–1,400 plants, which means that using manual air drying becomes a significant bottleneck. With demand skyrocketing, this is a major limitation to scaling up production to fully take advantage of this commercial opportunity.
Following are some of the common challenges with air drying:
- Requires a large amount of space for drying―roughly 2,000 square feet per acre
- Time to dry is from 3-10 days
- Difficulty in controlling the atmosphere for drying, especially as the square footage increases
- Labor-intensive process
- Inconsistent results in quality
- Pest management during the drying process
- Material loss due to mold and mildew
When you start to get to 50 acres of production and upwards, you’re going to run into a bottleneck if you’re still using air drying. These are your profits, and as a professional operation, it’s only natural to look at professional equipment. Different applications require different types of equipment. The following sections will give insight into the different types of technologies available and the appropriate applications of that technology.
Industrial Cannabis Processing
Whether you’re planting 100 acres or 1,000 acres, within 120 days of planting, the harvest is ready, and the equipment needs to be ready when the harvest comes in. And of course, there’s only so much control you have of the precise date of the harvest, depending on weather and soil conditions.
The type of thermal processing equipment and the process for drying the material will depend on the downstream use, whether that’s extraction, edible, smokable, performance fiber or other applications. There’s no one machine that is best for all applications. The biggest differentiation is smokable cannabis, which has specific processing needs that are different than the others. While smokable cannabis makes up a small percentage of the market, it’s easiest to understand, so we’ll address this first.
Thermal Processing to Retain Smokable Aesthetics
When it comes to drying cannabis flowers, the aesthetics are the number one priority. From Acapulco Gold to Purple Kush, customers come into the dispensary eyeing the product and looking for the perfect bud. Therefore, drying equipment for flowers needs to keep the material stationary, or at least limit the movement of the material, to prevent any aesthetic degradation. For this type of application, you’ll want to investigate equipment such as freeze dryers, tray dryers, industrial ovens or vacuum-assisted dryers. These technologies provide limited drying profiles based on the types of materials used. The main drawback is the throughput is slower than dryers with conveyers or agitation—but they are still faster than hang drying, and they will preserve the quality and aesthetics of the buds, as well as eliminate the risk of mold and mildew.
Benefits of Industrial Processing for Major Cannabis Applications
For the bulk of the cannabis market, that is, material dried for further downstream processing, the competitive advantage will go to those producers who have the most effective and efficient solutions. It’s no surprise that processors are looking at adjacent industries such as biomass, pharmaceutical, textile and food markets. Adapting tried-and-true technologies that are already producing high-quality materials is accelerating cannabis processors’ ability to leap ahead in their processing volumes. Proven solutions that can be rapidly adapted to cannabis include air-heated ovens, rotary dryers, microwave and combined heating and vacuum processing.
The advantages of industrial thermal processing equipment include:
- Terpene profile retention
- Higher CBD content per pound (hemp)
- Tight temperature control
- Low-temperature drying
- Uniformity of moisture content in materials post drying
- High degree of repeatability from batch to batch
Considerations for Thermal Processing
While thermal processing technologies have been used successfully in similar markets, it’s important to assess the technology considering the specific needs of your production line. As mentioned, each cannabis application is different, so make sure to perform due diligence before making this major investment.
Following are the major considerations to consider when looking at thermal processing technology for cannabis processing:
- Drying times: Ideally three hours or less
- Throughput: Batch size and ability for the equipment and manufacturer to scale with you as your business grows
- Total cost of ownership: Ongoing maintenance, cleaning and sanitizing, spare parts and downtime, plus the initial cost of equipment
- Equipment footprint: Floor space, environmental and safety requirements of the equipment
- Energy usage: Measurement in KW and BTUs, including warm-up and preparation time for machines
- Auxiliary equipment: Additional requirements, such as renewable liquids or other types of auxiliary equipment requirements
Testing
Every application is different. In rapidly emerging markets such as cannabis, it’s important to choose a thermal processing technology partner who allows you the ability to test material processing, preferably at both R&D and pilot scale sizes. If you’re building a supply line and the purchasing market changes, you may want to shift or add products that represent the wide variety of uses of cannabis, such CBD, medical, recreational and performance fibers. As you develop new materials, it’s important to be able to test equipment and parameters for optimizing output and quality.
Testing is beneficial for both the equipment vendor and the client.
- Equipment manufacturers develop their expertise and can create a partnership with their clients. Furthermore, vendors can ensure customer satisfaction by providing testing results that help their clients develop new products. Be wary of vendors who don’t want to spend that up-front time getting to know your needs.
- Customers leverage the testing process to get answers to their biggest questions and proof of concept. The risk is dramatically reduced by clear testing results that prove the quality parameters can be accomplished on a consistent basis. Also, by going through the testing process with your vendor, you’ll get a good idea of who you’re working with, who can solve your problems and where to go when you need new product development. You’ll be able to gauge the long-term viability of the relationship with the vendor, because thermal processing equipment can last decades. You want to know the vendor will be around for the long haul and isn’t just taking advantage of a new industry.
Experienced manufacturers generally will have test facilities available. Fully equipped test labs include small-scale testing for R&D as well as pilot-scale for large bulk drying needs.
Drying Curves
When it comes to thermal processing, articulating and demonstrating a drying curve is step one in establishing credibility as it relates to an application.
IMPORTANT NOTICE: If a manufacturer of thermal processing equipment can’t provide a sample drying curve of their performance, that’s a warning sign. Every experienced manufacturer will have this data available and will be able to provide you with proven testing of their equipment.
Ready For a Conversation?
Marion Process Solutions has over 80 years of experience working with clients in a variety of industries. Our insights have helped manufacturers drive innovation and deliver a competitive advantage in over 75 countries on six continents. If you’re looking to take your cannabis production to the next level, contact Marion Process Solutions.