3 Horizontal Mixer Design Features that Optimize Performance
Three Key Considerations for Selecting Horizontal Mixing Equipment
When it comes to mixing and blending, as in any established industry, the fundamentals can easily be taken for granted or, worse yet, completely overlooked.
We'd like to argue the case for the basics of mixing and blending technology. Focusing your attentions on the integral features of horizontal mixing equipment is just as important as the granular details. No amount of bells and whistles will detract from poor quality or design.
Mixers come in many shapes, sizes, and levels of sanitation. This article focuses on three key elements of general horizontal mixer configurations: agitator design, shaft configurations, and sealing technologies.
Agitator Design | Does It Really Matter?
Spoiler alert: it does. In fact, this may very well be the most important decision you’ll make for your mixer. Selecting the agitator design best suited to your application is key in ensuring optimal blending, mix times, and effective material evacuation at discharge.
Paddle Agitators
The configuration of a paddle mixer lends itself well to mixing solids with a range of particle sizes, densities and viscosities, and offers easier access for cleaning in between batches. Its scooping, lifting, and tumbling motions provides gentle and precise mixing of product. Product is continuously mixed in a distinct, three-dimensional figure-eight pattern, pulling material in from the outer mixer bed into the center, where the mixing action is centralized and most aggressive.
Double Ribbon Agitators
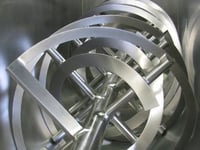
Hybrid Agitators
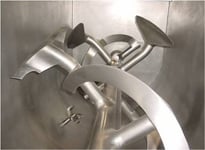
Hybrid mixers combine the tumbling action of paddle mixers with the rolling pattern of ribbon mixers to create a double-reversing mixing effect. This increases the energy being transferred into the product. Hybrid agitators are a good fit for materials that tend to build up in the center of the mixer, as the combined mixing action promotes even product levels within the trough.
Fluidizing Paddle Agitators
Fluidizing Paddle Mixers provide sophisticated, dual-directional mixing action with multiple paddles. Fluidized mixing, through a combination of inward and outward motions. Fluidized paddle mixing technology is an excellent choice for bakery blends, nutraceuticals, detergent powders, and more.
Shaft Configuration | Seven Foundational Factors
Compromising on the configuration of your mixer's shaft will negatively impact the performance, maintenance requirements, and the long-term productivity of your mixing equipment. When considering new mixing equipment, there are seven key technical features that should be closely analyzed and vetted:
- Shaft Diameter: Shafts with smaller diameters will have higher stress concentrations and, as a result, are more prone to breaks from fatigue failure.
- Static Deflection: The shaft acts as a continuously loaded and simply supported beam. Excessive deflection promotes metal fatigue and speeds up seal wear.
- Dynamic Deflection: Excessive deflection due to dynamic loading increases clearances between the agitator and the trough on the down-sweep side of the mixer; solid shaft designs (mentioned below) will have less deflection compared to hollow options, promoting better mixing.
- Reduced Stress Risers: The use of stress risers should be minimized in order to avoid metal fatigue or potential shaft breakage.
- Solid, One-Piece Shaft: This design consideration reduces stress and minimizes agitator deflection.
- Shaft Straightness: Welded shafts that are not re-straightened at the end of the fabrication process are prone to excessive warping. This will ultimately accelerate the wear of seals and bearings, creating higher long-term maintenance costs.
- Paddle or Ribbon Clearance: Large and/or irregular gaps between agitator blades or ribbons translate to higher coefficients of variation and longer mixing times. This will directly impact mixing performance.
Interested in an in-depth examination of the seven key principles of shaft design?
Sealing Technologies | Insurance for Your Investment
Utilizing the correct seals and preventative maintenance program for your mixer will protect and extend the life of your equipment. Seal choices can range from simple braided rope packing inside of a barrel-housing to mechanical seal options. Thanks to recent advancements, lip seals comprised of composite materials are available that offer better performance and sanitation than traditional packing seals, and are overall more affordable than mechanical seals.
Benefits of Lip Seals in Composite Materials
- Non-porous material (unlike packing, which can retain media)
- Shaft-friendly materials prevent premature wear
- Easier, quicker maintenance
- Longer-lasting and resistant to degradation
- Cleanable and reusable
- Sanitary: FDA compliant and 3-A certified
- Proven longer run times
- More cost-effective than mechanical seals
Minimize downtime expenses and the potential for product contamination or leakage by selecting the right seal for your application. Taking a "one size fits all" approach to mixer seals can turn out to be a costly mistake.
Learn more about Marion's Smart Solutions for Better Shaft Sealing.
Conclusion | Getting Started
When in the market for a new horizontal mixer, be sure to consider the basic elements of agitator design, shaft configuration, and sealing technologies for your operation. Keeping the fundamentals top of mind as you configure your mixer will ensure the end result is built to support your needs.
So... what's next? The optimal configuration of your mixer starts with a professional consultation. Your chosen equipment manufacturer should understand the importance of determining these key design elements listed above as your partner in crafting a cost-effective, high-performance mixing solution. Taking mixing 101 into consideration early on in the process will ensure your end result will provide years of optimal performance and satisfaction.
Originally shared on Powder & Bulk Solids on January 19, 2016. Click here to read the article.