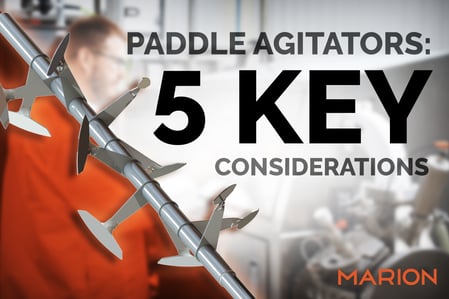
When it comes to horizontal mixer design, the type of agitator you choose is almost as important as the mixer itself.
In the world of industrial mixing equipment, there are four main types of agitators: paddle agitators, fluidizing paddle agitators, ribbon agitators and hybrid agitators.
Because agitator design directly impacts mixing time and blend quality – and production efficiency and operational costs by extension – you’ll want to choose wisely.
Each of the four types of agitators provide advantages that can help you shorten mixing time, improve production and reduce costs. But what makes one choice better suited for one application over another?
When looking specifically at paddle agitators, there are five basic things you should consider to help you determine if adding one is a smart option.
Mixing Characteristics
Defining mixing requirements is a critical first step for selecting the right mixing agitator, according to Lee Girard, a senior design engineer at Marion Process Solutions.
“‘Is the material a solid-liquid mixture, a liquid-liquid blend or a combination?’ is one of the first questions we ask at Marion,” explains Girard. “The physical state and properties of the material, such as particle size, viscosity, density and phase compatibility, will help determine how well an agitator can meet your specific mixing needs.”
Paddle agitators perform well with materials of dissimilar size, shape and density. They are ideal for fragile applications and can handle a wide range of material viscosities from low-viscosity liquids to high-viscosity pastes, and other applications that require mixing solids with wet ingredients.
“One area where paddle mixers can fall short is separating clumps,” Girard added. “If this is desired, a ribbon or hybrid style agitator may be the better fit.”
Batch Capacity
Having an idea of the volume of material that needs to be processed is another important criterion in selecting a mixer agitator. Do you plan on filling your mixer to capacity with every batch or are you in the piloting phase of production and would like the flexibility to run smaller volumes?
“Paddle agitators can work effectively when filled to as little as 20% of rated capacity, which provides additional flexibility for operations that are not yet ready for full scale production,” Girard said.
Mixing Speed
Matching mixing speed and the intensity of the mixing action should be closely linked to your material’s mixing characteristics, according to Girard.
Some materials may require aggressive mixing that can be handled more efficiently by a fluidizing paddle design, while others can benefit from the gentler approach of a standard plated paddle agitator.
The gentle sweeping motion of a paddle agitator makes for effective blending of materials without excessive turbulence, shear and mechanical stress.
“This helps to ensure the final product retains its desired properties,” Girard said. “For certain materials that are shear sensitive, like polymers, powders and some chemicals, paddle agitators can help minimize changes in their properties or performance.”
While ribbon agitators are better at separating clumps, they can take longer to produce a uniform mix than a standard paddle or fluidizing paddle agitator.
Cleaning and Sanitation
When it comes to sanitation requirements for agitators, more design complexity and surface area can sometimes mean additional labor time between mixing campaigns.
Plated paddle designs are generally the easiest out of the different styles of agitators to clean. While ribbon and hybrid ribbon-paddle agitators have their advantages when it comes to specific applications and mixing requirements, they are generally more time-consuming to clean than paddles.
It’s important to note that not all paddle designs are created equal, notes Girard.
Some manufacturers may still use a bolted paddle design, which features hard-to-reach nooks and crannies that can be difficult to clean thoroughly and become breeding grounds for bacteria.
“You should look for paddle agitators that are welded together or better yet, cut from a single piece of stainless steel for optimum sanitation and low-maintenance cleanability,” Girard said.
Cost Considerations
Out of the different styles of agitators, standard paddles generally come at a lower cost than ribbon or hybrid agitators due to their simple design. Fluidizing paddles are typically the most expensive because they require a more robust motor to reach the desired RPMs for a more aggressive and faster mix.
That said, there are many factors that go into mixer design, so you shouldn’t base your choice of agitator on the upfront cost alone.
“To make the best recommendation, we like to get as much detail from our customers as possible,” Girard said. “That is why we encourage them to test their material in our machines before they buy.”
At the end of the test, customers get a detailed report showing how well a recommended mixer configuration can lead to quality improvements, such as increased throughput or reduced mixing time.
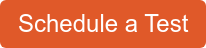
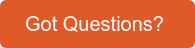
Additional resources:
Three Considerations for Selecting Horizontal Mixing Equipment
Choosing the Right Agitator for Your Application
When Does Refurbishing a Mixer Make More Sense than Buying New?
5 Things to Look for in a Quality Cover for a Mixer